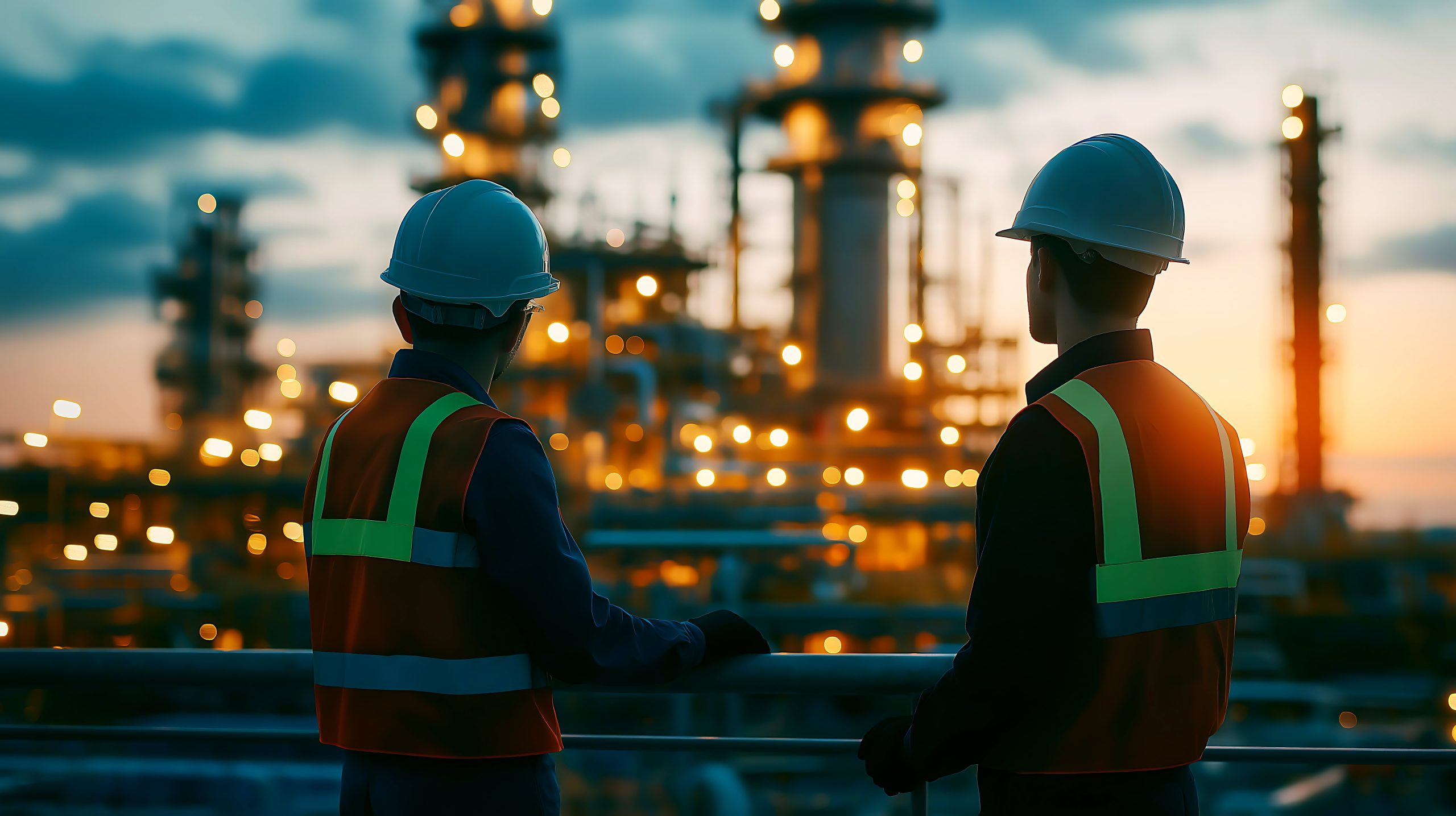
Your safety is our priority, wherever you are
From gin distilleries to battery energy storage systems, we work across a vast array of businesses and industries to keep people and property safe from gas hazards.
Whatever your needs, we can tailor our gas and flame detection solutions to provide complete peace of mind.
Industries We’ve Worked With
With a wealth of experience across clients such as oil refineries to gas plants, Crowcon is trusted across the sector to provide top-tier gas detection and monitoring as well as flame detection support across upstream, midstream and downstream operations.
From helping pioneer the safety of the hydrogen power supply chain, to developing cutting-edge technology to detect off-gassing of lithium-ion batteries, we work across the renewable energy industry to help protect and advance a more sustainable energy future.
Across the marine sector, multiple gas hazards are present from factors such as accumulation of CO and NOx from vehicle exhausts on ferries, to vapour emissions on cargo tanks. We work across the marine industry to provide cas detection and monitoring across all vessels and applications.
The water industry frequently involves wet and dirty environments, with multiple toxic and flammable gas hazards and the risk of oxygen depletion. Whether a facility focuses on the production of clean, portable water or treating effluent, Crowcon is proud to serve a wide variety of water industry clients, providing gas detection equipment that keeps workers safe around the world.
The highly flammable nature of petrochemicals makes a rigorous approach to gas detection of paramount importance. Methanol, ethylene, propylene, butadiene, benzene, toluene and xylenes (BTX) may be the building blocks of many consumer goods, but without care they pose a significant risk to human life. This makes rigorous attention to gas detection and monitoring crucial for safeguarding the lives of the hundreds of thousands of workers in this sector.
From breweries to chemical disinfection of storage sites, the food and beverage industry is exposed to a plethora of hazardous gases which can be toxic, flammable, or both. We’ve worked with household names to safeguard against these harms and are experienced in doing so across the food and beverage supply chain.
Heating, ventilation, air conditioning and refrigeration require use of liquids and gases to operate, many of which are highly flammable or toxic- as well as harmful to the environment. This means careful monitoring is essential, not only because of the potential harm to human life, but the negative environmental impact of HFCs and PFCs, too.
While many industries that work with or around hazardous gases have safety standards they need to comply with, businesses in general industry may not. That’s where the expertise of the Crowcon team is invaluable, helping optimise safety and identify hazards to safeguard both your personnel and your property from harm.
Workers in the construction industry are at risk from a wide variety of hazardous gases, from carbon monoxide to methane and other volatile organic compounds (VOC’s). Construction is a large contributor to the emission of toxic gases into the atmosphere, which also means construction personnel are more at risk of harm. Crowcon is trusted around the world to provide specialist high-quality equipment to protect workers from these toxic and flammable gases.
Subscribe to get the latest insights
IN your INbox
Read about Crowcon’s Privacy and Cookie policy here. If you change your mind, you can unsubscribe at any time