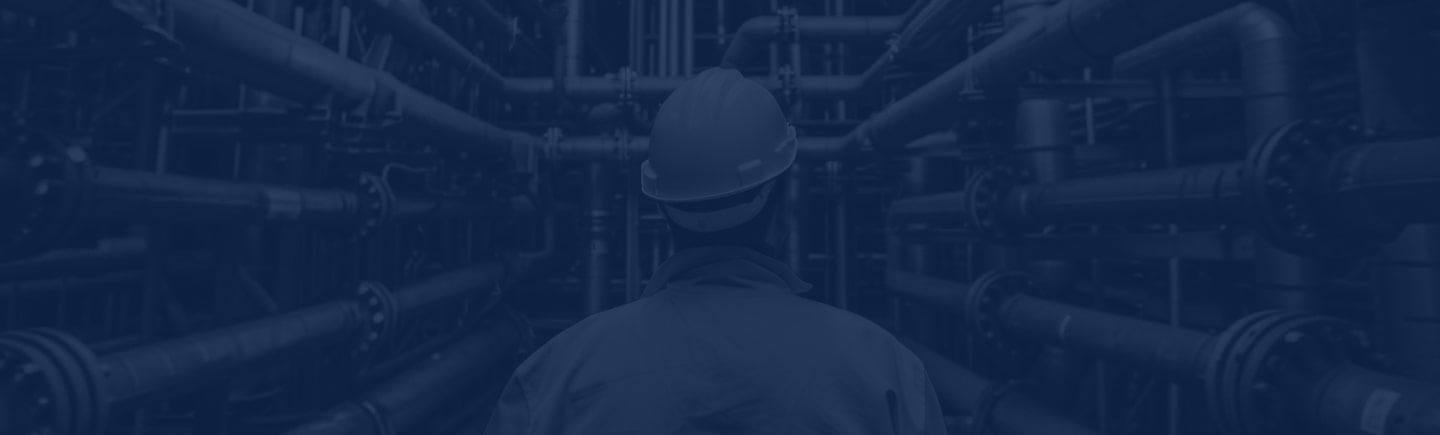
“Safety is our number one priority and we need to ensure that we detect any leaks at the earliest stage. While the electrolyser has in-built capability to shut down immediately, Crowcon provides an important line of defence both inside the container, and through the mobile monitor worn by our operatives on site.”
Will Stinton
Head of Operations at Protium
Whatever your gas detection needs, we have the solution
Environmental factors, square footage, and ventilation are all factors that can impact what gas detection technology is needed for your space, and it can feel like a mine-field. That’s why for more than 50 years, Crowcon has been helping businesses of all sizes and industries around the world stay safe with our gas detection products, solutions, and services. Our wide portfolio includes everything from fixed and portable gas detectors to flame detection and air quality monitoring systems.
Asset Management
Keep track of multiple portable detectors on site all in one place with Crowcon Connect asset management. The only connected safety software that works on existing and new Crowcon portable detectors, Crowcon Connect provides total site visibility and full control over your gas detection data.
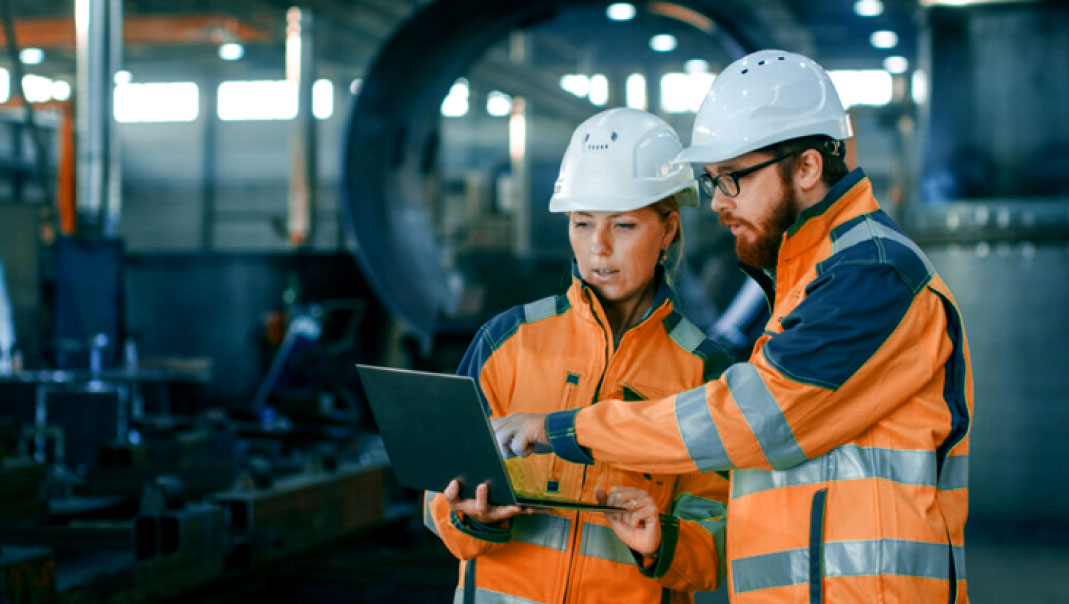
Case Studies
Want to talk?
Whether you’re crystal clear on what your site needs to stay protected from gas hazards, or are just on a fact-finding mission, our team is always happy to help.
Book an obligation-free call with one of our experts, and find out more about how we can help keep your people and property safe.
Read about Crowcon’s Privacy and Cookie policy here. If you change your mind, you can unsubscribe at any time