Gas Hazards in the Water & Waste water Sector
Gas detectors must be chosen to suit the specific environment in which they operate. The water industry frequently involves wet and dirty environments, with multiple toxic and flammable gas hazards such as methane, carbon dioxide, and the risk of oxygen depletion posing significant risks.
Here are just some of the core gas detection risks often found in water and wastewater industrial environments.
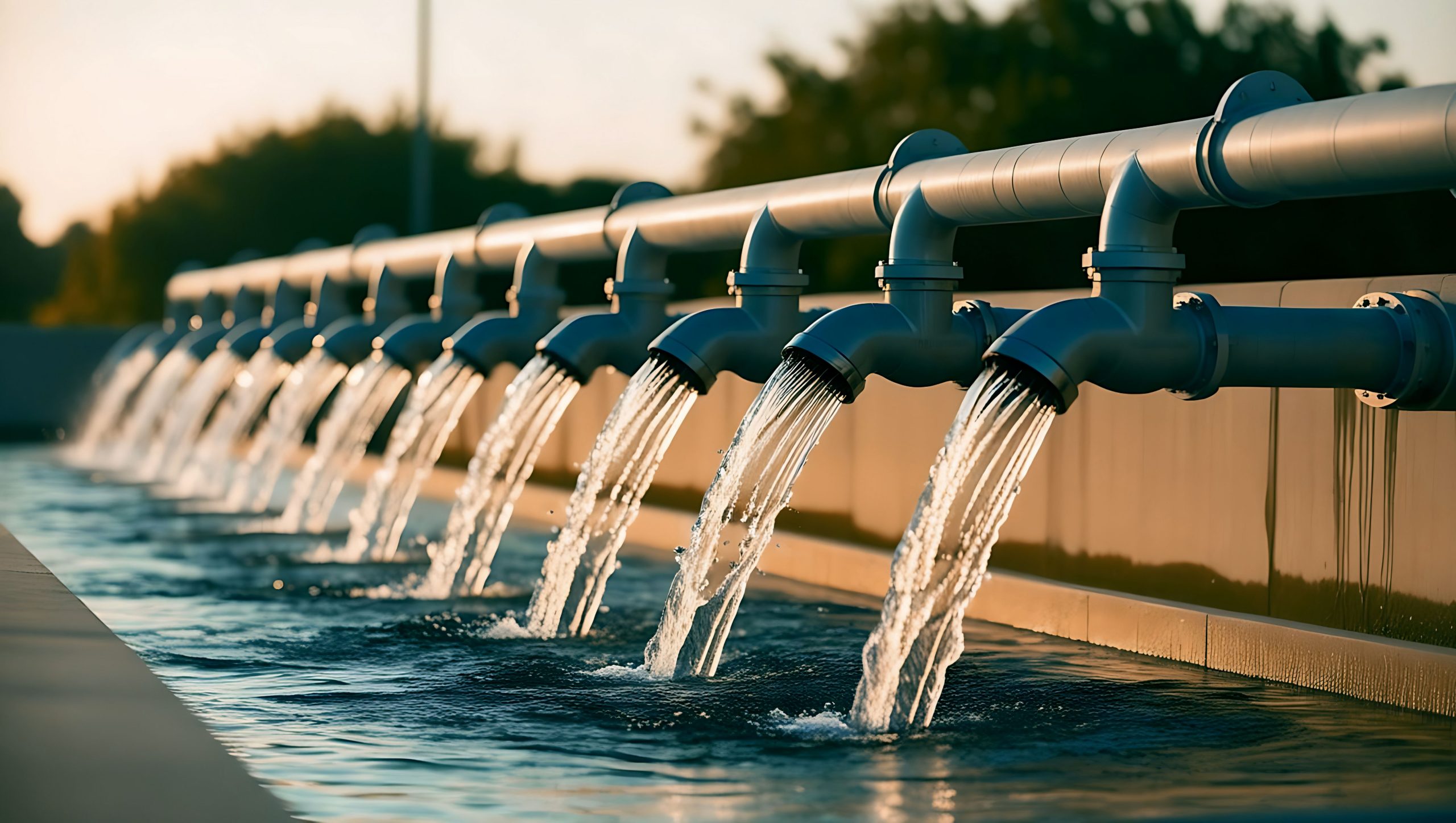
Water Purification
While it might be surprising, the process of water purification relies on poisonous gases like ozone, chlorine dioxide, and carbon dioxide the create clean, drinkable water. Carbon dioxide, for example, is used to maintain acidity levels, while ozone and chlorine are used for disinfection of water.
While essential, these gases present serious health risks to those working in water purification if exposure is not properly managed. Similarly, in wastewater treatment, hazardous gases such as methane and hydrogen sulphide are produced during the decomposition of sewage remains. Methane is highly flammable and creates a risk of asphyxiation, while hydrogen sulphide is toxic and corrosive, posing serious risk to life in wastewater plants, sewage systems, and pumping stations. Therefore portable single- and multi-gas detectors, as well as fixed gas detection systems, are essential for ensuring safety during operations in water treatment and wastewater management facilities.
Detectors and Control Panels for the Water & Waste water Industry
Portable Monitors
Fixed Monitors
Flame Detection
Control Panels
European Regulations on Gas Detection
European Commission Directive 2017/164 (EU Directive 2017/164) issued in January 2017, established a new list of indicative occupational exposure limit values (IOELVs, as the directive calls them) in the workplace. The list includes carbon monoxide, sulphur dioxide, hydrogen cyanide, manganese, diacetyl and many other chemicals. Member states were required to enact the relevant laws, regulations and administrative provisions to comply by late August 2018.
RELATED Insights
Want to speak to the experts?
No one understands better than our team just how important the right detection solutions are for you and your site. That’s why we’re always on hand to talk you through your gas detection needs, to ensure you’re equipped with precisely the right tools to keep your people and property safe.
Read about Crowcon’s Privacy and Cookie policy here. If you change your mind, you can unsubscribe at any time